Założenie firmy Wtedy wszystko się zaczęło. Pięć osób pracowało w niewielkim zakładzie w Ursusie gdzie dokładało elementy dodatkowe do aut.
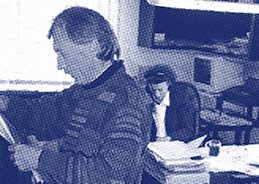
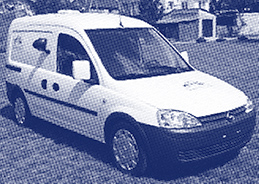
Pierwszy importer Rozpoczęliśmy oficjalną współpracę z Oplem.
Pierwszy bankowóz
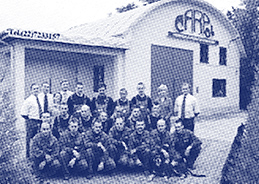
Nowe miejsce Przenieśliśmy się do Reguł pod Warszawą. Tam została wynajęta hala, która zatrudniała już 40 osób.
Nowi klienci Zaprezentowaliśmy nasze produkty na Międzynarodowych Targach Budma w Poznaniu. Rozpoczęliśmy współpracę z nowymi importerami.
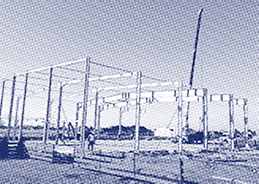
Pierwsza halaW dwa lata od zakupu terenu pod inwestycję, powstała pierwsza hala produkcyjna.
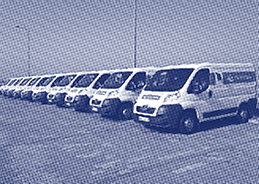
Rozbudowa Na potrzebu kontraktu dla Poczty Polskiej (ponad 900 aut), wybudowaliśmy drugą halę, a wraz z nią zakupiliśmy znaczący park maszynowy. W jego skład wchodziły m.in.: termo formierki, prasa krawędziowa, ploter pięcioosiowy, roboty spawalnicze.
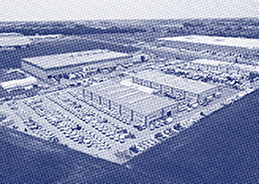
Nie zatrzymujemy się Rozpoczynamy budowę trzeciej hali. Będzie gotowa w roku 2014.
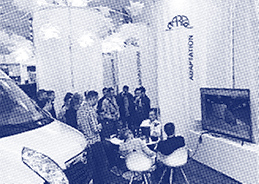
Sukces Wystawiliśmy się z własnym stanowiskiem na Targach w Hanowerze.
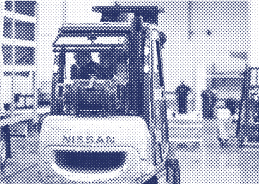
Sukces 2020 rok to nasz ogromny sukces. Żaden pracownik, z powodu pandemii Covid 19 nie stracił pracy.
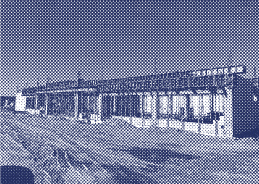
Obchodzimy 25-lecie Z tej okazji powiększamy naszą firmę o kolejną halę.